Во время работы волоконного лазерного станка в место реза через сопло подаётся газ, участвующий в процессе обработки заготовок лазерным лучом. В этой статье мы поговорим о газах, применяемых для лазерной резки металла, о том, какие из них являются более предпочтительными, а также расскажем о других часто возникающих вопросах, связанных с этой темой.
Как выбрать газ для резки металла?
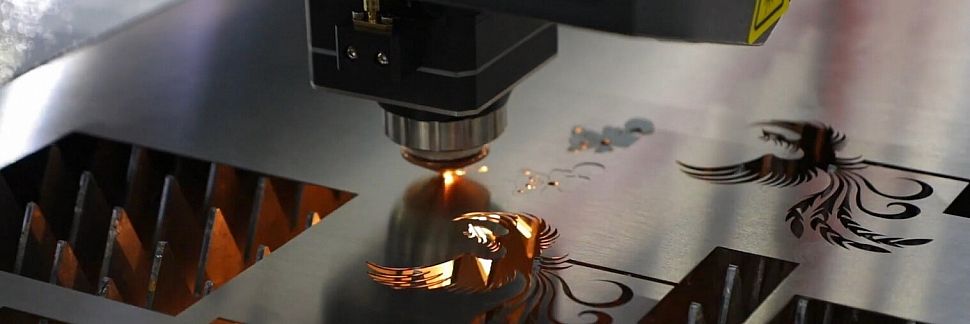
Прежде чем перейти к теме выбора подходящего газа для резки металлических поверхностей мы перечислим основные газы, применяемые с этой целью:
- Воздух;
- Кислород (активный газ);
- Азот (инертный газ);
- Аргон (инертный газ).
При выборе газа для волоконной резки металла в первую очередь стоит ориентироваться на характеристики обрабатываемого материала и толщину листа. Для резки чёрных металлов с относительно небольшой толщиной (менее 3 мм) может хорошо подойти предварительно прошедший процесс сжатия и очистки воздух, а для чёрных металлов с толщиной более 3 мм стоит применять кислород. В случае с алюминием, латунью и нержавейкой, стоит применять более дорогой очищенный азот, ведь использование воздуха или кислорода при работе с этими металлами приводит к их перегреву, что существенно снижает качество реза и приводит к утрате ими структурной устойчивости и окислению. Азот хорошо подходит для лазерной резки большинства цветных и чёрных металлов с различной толщиной и положительно сказывается на качестве резки, но из-за его высокой цены целесообразнее применять его лишь при резке первых. Приятным бонусом при использовании азота является его охлаждающее действие на режущую кромку. Но не для всех целей прекрасен азот - при резке титана требуется определённый газ, который не приводит к изменению его свойств, - аргон.
Чистота газа оказывает большое влияние на качество резки, поэтому лучшим выбором станет газ с чистотой около 99,9%. Для лазерной резки может использоваться и азот с чистотой от 99,5%, но даже в этом случае будет заметно снижение качества реза.
Расход газа и давление при резке

На расход того или иного газа при резке металла волоконным лазером влияют следующие факторы:
- Вид используемого газа;
- Давление;
- Толщина материала;
- Сопло.
В связи с тем, что кислород является активным газом, он применяется с меньшим уровнем давления, чем при использовании азота и воздуха, что снижает его расход. При работе с кислородом необходима точная регулировка давления - после пробития металла важно повысить давление, иначе вы рискуете получить брызги раскалённого металла при резке. Для контроля уровня давления вам понадобится особый регулятор. Давление при работе с кислородом не превышает 1 атм, а при использовании азота уровень давления обычно не выше 20 атм.
Хранение газа
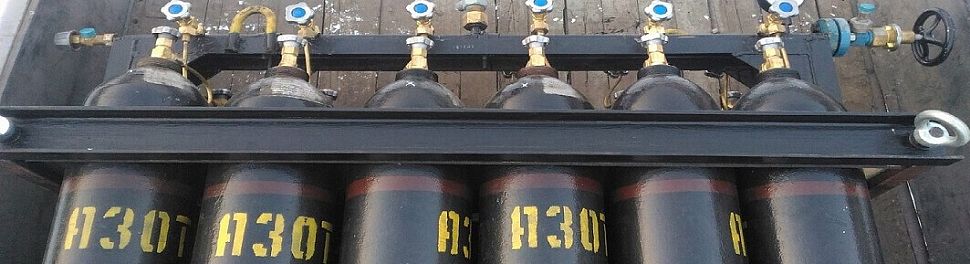
После выбора необходимого нам газа, возникает следующий логичный вопрос: «В каком виде стоит приобретать газ?». Для хранения кислорода, азота или аргона используются баллоны (40-70 л), моноблоки баллонов (состоят из нескольких средних баллонов – от 4-х и более) и криоцилиндры (вариант, сочетающий в себе компактность, чистоту и большой объём хранимого газа). При выборе между этими вариантами стоит задуматься о том, как часто будет использоваться ваш станок, ведь на постоянную смену одиночных баллонов при большом объёме производства будет уходить слишком много времени, и в таком случае лучшим вариантом станет приобретение моноблока или криоцилиндра.
Особенности при работе с воздухом
Как мы и упоминали выше, для резки металла может использоваться только воздух, предварительно прошедший процесс сжатия и очистки. Для этого требуется воздушный компрессор и фильтры, предотвращающие загрязнение станка парами масла и влаги. Такое оборудование является довольно дорогим и требует периодического обслуживания – своевременная замена фильтров и масла в данном случае имеет большую важность. Дешёвые компрессоры и фильтры довольно быстро выходят из строя, поэтому рекомендуется внимательнее подходить к их выбору. Винтовой компрессор с объёмом ресивера от 500 литров, давлением от 15 бар и производительностью от 800 л/мин будет отличным надёжным вариантом, если не сильно экономить при выборе.